History and Applications Using MIL-STD-810
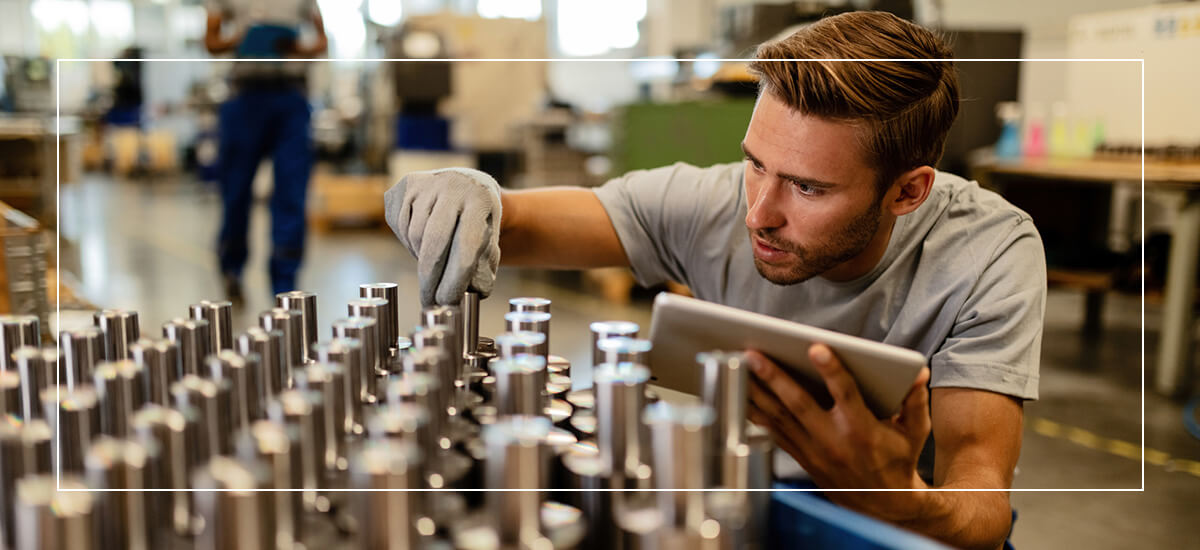
The military standard has been in effect for decades, providing guidelines and testing procedures for various components to ensure they can operate under challenging military conditions. Over time, the standard’s stringent testing filtered into the commercial arena, acting as a comprehensive form of quality control for original equipment manufacturers (OEMs) and end users in various industries.
Even the smallest components provide a vital function in military, aerospace and industrial environments. Something as simple as your choice of telescopic slide could impact your entire operation. Ensuring these various components meet military standard 810 and any other relevant standards can give you the confidence to operate, even in the most challenging conditions.
What Is the Military Standard?
The Military Standard, or MIL-STD, ensures products and components meet specific requirements for defense-related purposes. It’s enforced by the U.S. Department of Defense (DOD) and maintained by the Army, Navy and Air Force. Although created for military use, MIL-STD is used across many organizations due to the strongest test methods used to determine components’ suitability for use in extreme conditions.
Many military standards exist, including military standard 810, covering various products and components under a broad range of environmental conditions.
What Is MIL-STD-810?
MIL-STD-810 is one of the most widely used military standards. It emphasizes tailoring a product’s environmental design and testing it under conditions that replicate the environments in which it is expected to perform. The standard and test methods aim to define environmental stress sequences and levels of equipment life cycles. They are often used to develop test criteria to ensure equipment maintains its longevity under challenging conditions.
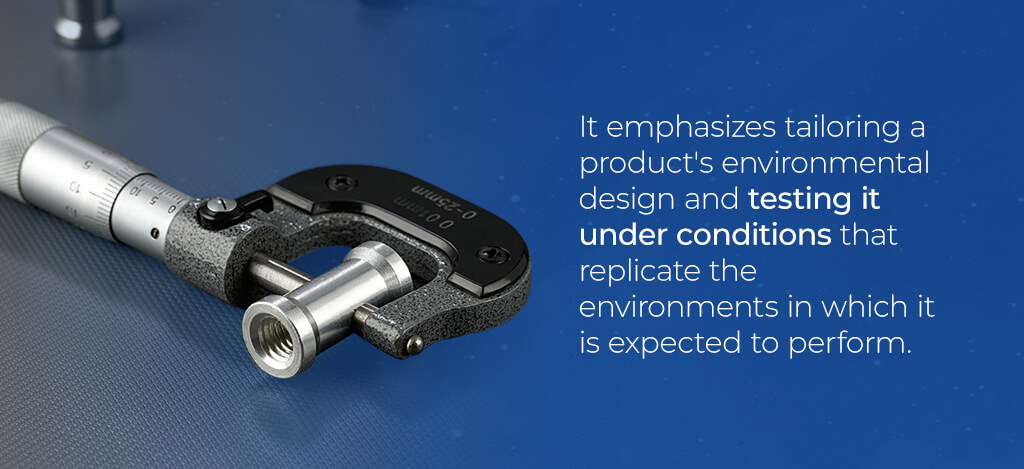
The standard addresses various environmental conditions, including pressure and temperature variations, temperature shock, humidity, fungus, rust, sand and dust. It describes environmental management and engineering processes that can impact the safety of military personnel under potentially hazardous conditions.
The first iteration of MIL-STD-810 came into effect in 1962 and has been revised several times since then. The most well-known revision is likely the MIL-STD-810G military standard. However, the most current version of the standard is MIL-STD-810H, which has been in effect since 2019.
MIL-STD-810 Testing
MIL-STD-810 test methods cover an impressive number of challenging conditions. The following table provides an overview of the various test methods and their scope:
TEST METHOD | DESCRIPTION | SCOPE |
---|---|---|
Test Method 500 | Low pressure (altitude) | Determines whether a component can maintain operation in a low-pressure environment or withstand abrupt pressure changes. |
Test Method 501.5 | High temperature | Evaluates the performance of a product or component in high temperatures, and assess the effects of these temperatures on various components. |
Test Method 502.5 | Low temperature | Ensures material functionality during low temperatures during storage and operation. |
Test Method 503.5 | Temperature shock | Determines the effect of sudden temperature changes on products and components. |
Test Method 504.1 | Contamination by fluids | Ensures the proper performance of products during temporary, intermittent or consistent exposure to liquids. |
Test Method 505.5 | Solar radiation | Evaluates the effects of direct sunlight exposure on products or components. |
Test Method 507.5 | Humidity | Places components in hot, moist environments to measure the effect of humidity on system operations. |
Test Method 506.8 | Fungus | Tests how various systems work if fungal growth impacts the materials or performance. |
Test Method 509.5 | Salt fog | Ensures components continue to function in the presence of salt, which can cause corrosion. |
Test Method 510.5 | Sand and dust | Tests rugged products and systems, measuring the reliability of filters in keeping sand and dust away from critical components. |
Test Method 511.5 | Explosive atmosphere | Measures whether components can function in a fuel-air atmosphere without triggering an explosive reaction. |
Test Method 512.5 | Immersion | Assess whether components can perform acceptably when immersed in water. |
Test Method 513.6 | Acceleration | Determines whether components can function when involved in high accelerations in an aircraft. |
Test Method 514.6 | Vibration | Ensures that rugged components function optimally through vibrations. |
Test Method 516.6 | Shock | Measures the effectiveness of components in withstanding shock throughout transportation and operation. |
Test Method 517.1 | Pyroshock | Tests the performance of components in the presence of nearby explosive shock. |
Test Method 518.1 | Acidic atmosphere | Assess how well products and their coatings can withstand corrosion in the atmosphere during storage and operation. |
Test Method 519.6 | Gunfire shock | Measures how well products and components can withstand the vibrations associated with short bursts of gunfire vibrations. |
Test Method 520.3 | Temperature, humidity, vibration and altitude | Measures a product’s performance when exposed to combined environmental factors on aircraft and ground vehicles. |
Test Method 521.3 | Icing or freezing rain | This test method validates components under freezing conditions. It also outlines methods operators can use to defrost the system without causing damage. |
Test Method 522.1 | Ballistic shock | Tests products against abrupt shifts in momentum. |
Test Method 523.3 | Vibro-acoustic or temperature | Exposes components to multiple test factors simultaneously, focusing on external aircraft storage during flight. |
Test Method 524 | Freeze and thaw | Tests system performance when it freezes over and then begins to thaw, evaluating the effects on overall structure and performance. |
Test Method 525 | Time waveform replication | Establishes how long a system can function in its environment before changes occur. |
Test Method 526 | Rail Impact | Ensures components can withstand impact during ground transport. |
Test Method 527 | Multi-exciter | It replicates a complete environment, simultaneously applying multiple environmental stressors to a component to determine how long it takes to show changes or signs of fatigue. |
Test Method 528.1 | Mechanical vibrations of shipboard equipment | Evaluates equipment on ships to determine the effects of external or internal vibrations. |
Users can conduct the most relevant tests depending on the system or product. Certified labs conduct these tests, and they are well-versed in the flexibility of the tests for commercial and military applications.
What Is a Roller Drawer Slide and How Does It Relate to MIL-STD-810?
A roller drawer slide is a linear motion solution that smoothly opens and closes equipment drawers in a low profile. They consist of two components — a cabinet and a drawer member. These two components glide over one another to facilitate easy opening and closing. These slides offer many benefits in the aerospace and defense industries, where they are a common choice for aircraft seat systems, equipment racks and missile systems.
These slides may be tested for military and other high-level applications to withstand challenging operating environments. Testing these components ensures their durability and performance in various conditions. Many pieces of military equipment use roller slides to store sensitive components. These slides must undergo MIL-STD-810 testing to ensure they can endure field conditions without failing, boosting equipment reliability and functionality at the most critical times.
Trust Jonathan Engineered Solutions for Your Linear Motion Requirements
Choosing telescopic slides for challenging conditions can maintain operational efficiency and save your organization money. When your linear motion solutions suit the intended application, they maintain longevity and keep critical products and components secure during transit.
With ISO 9001:2015/AS9100D certifications, Jonathan Engineered Solutions is a leading manufacturer of ball-bearing slides and other critical components, including rugged assemblies. We can provide you with a custom product or assembly suited to your needs. Our experienced teams remain committed to excellence in motion, and every JES client works alongside an assigned expert to handle your account requirements. Please request a quote from us and elevate your next operation today!
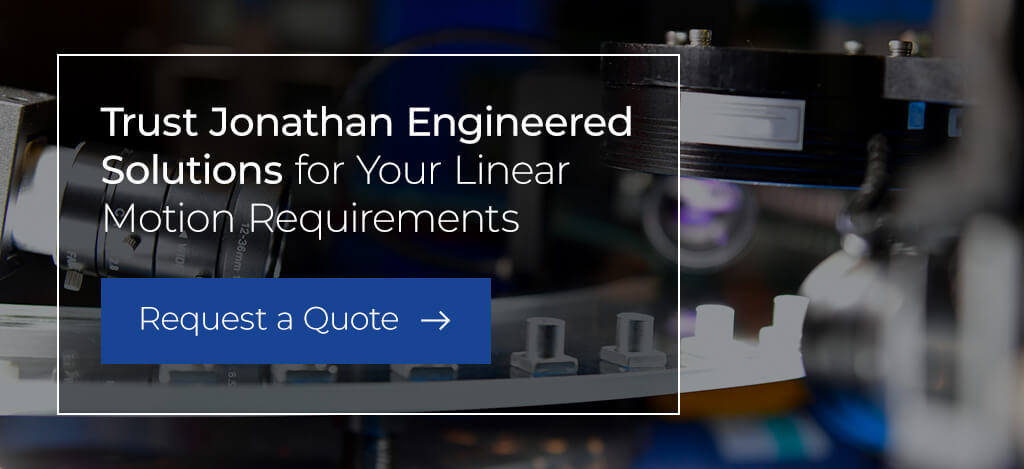
Speak with a Sales Representative
Our representatives have a wealth of knowledge on all our products – let them steer you in the right direction.
Learn More